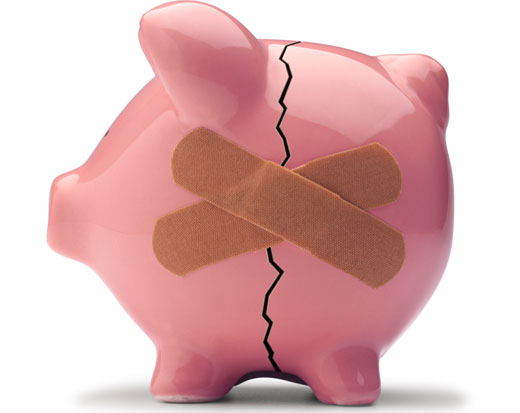
7 İsraf (7 Waste – Fazla Üretim, Fazla Stok, Taşıma, Kusurlu Üretim, Gereksiz İşlem, Gereksiz İnsan Hareketi, Bekleme), üretim alanında değer katmayan işlemleri sınıflandırma ve inceleme yöntemidir. Aynı yöntemi ofis içinde de uygulayabilirsiniz.
İsrafın eliminasyonu en temel iyileştirme yöntemidir. Yoğun ve baskı altında çalışanlar bu tip yöntemleri çoğu kez ve hatalı olarak “fazla teorik” görürler; yöntemlerin faydasını onaylamakla birlikte “onların kendileri için değil, başkaları için olduğu” inancı içinde olurlar.
İsrafın eliminasyonu bir çok yöntemin uygulanması ile mümkün olabilecek bir sonuçtur. Gerçekleştirebilmek için hem yöntemler hakkında bilgi edinmeli hem de bıkıp usanmadan uygulamaya çalışmalısınız.
İsraf 1 : Fazla Üretim
- Gereğinden fazla bilgi ve döküman üretimi, gereğinden fazla detay.
- Müşterinin tam olarak ne istediğini bilmeden veri üretmeye çalışmak
İsraf 2 : Gereksiz Stok
- Gereğinden fazla dökümana sahip olmak, ekstra kopyalar, ekstra dosyalar (örneğin farklı yöneticiler için farklı dosyalar).
- Gereksiz ofis malzemesi, yıllarca kullanılmayacak ekipman veya dökümanların depolanması
İsraf 3 : Taşıma
- Bir yerden bir yere bilgi ve malzemeleri aktarma sonra geri aktarma
- Birden fazla inceleme ve onaylama için dolaşmak
- Kötü ofis tasarımı ve merkezi arşivuygulamaları ile dosya ve belgelerin sık ve uzun mesafelerde taşınması
İsraf 4 : Kusurlu Üretim
Seminer : Maliyetinizi Nasıl Azaltacak, Şirketinizde İsrafı Nasıl Yok Edeceksiniz ? Kaizen Örnekleri ve Yalın Üretime Giriş (Lean 101)
.
Bu seminerde Lean Manufacturing / Yalın Üretim yaklaşımının en temel noktası olan ?İsrafın Yokedilmesi ? Removing Waste? başlığını inceleyecek, maliyetinizi nasıl adım adım azaltabileceğinizi göreceksiniz.
İsraf Nasıl Yok Edilir (How To Remove Waste) semineri uygulanabilir bilgi ile donatılmıştır, seminerden hemen sonra öğrendiklerinizi kullanarak şirketinize katkıda bulunmaya başlayabilirsiniz. Elde edeceğiniz yol haritası size ömür boyu yol gösterecek, her gün yeni bir faydayı bulup ortaya çıkartmanızı sağlayacaktır.
Maliyeti azaltmak için ne yapmayı planlıyorsun ?
Verimliliği arttıracağım
Yarın sabah ne yaparak başlamayı düşünüyorsun ?
Mevcut durumu inceleyeceğim
Sonra ne olacak ?
Operasyonlar gereken hızda yapılıyor mu anlayacağım
Sonra ne olacak ?
Yavaş olanları hızlandıracağım
Yavaş olan yok ise ne yapacaksın ?
Umarım vardır ..
Bu yaklaşım biçimini benimseyenler, zaten yaptıkları , belki de en iyi yaptıkları bir aktiviteyi “nasıl daha iyi yaparım” diye düşünür. Elbetteki değerli bir çalışmadır ancak bir çok durumda “yarın sabah maliyeti azaltmak için ne yapmalıyım” sorusuna cevap vermez. Zaten bu tip bir analizin sağlayacağı maliyet azalması en fazla % 1-3 arasında olabilir, belki de hiç olmaz.
Bu tür çalışmaların sonucunda Birim Maliyetiniz düşmüş gibi görünebilir ancak sizin toplam maliyet hiç değişmiyor hatta artıyor bile olabilir (Nasıl Artar !). Dolayısı ile harcanan kıymetli zamanın karşılığında sadece yorgunluk daha önemlisi ileride yapılabilecek çalışmaları engelleyecek olan düş kırıklığı yaratılır.
İsrafın yok edilmesi, Yalın Şirket / Yalın Üretim yaklaşımının en temel noktasıdır. İsraf konusu ve ilgili yöntemler yeterince iyi anlaşılmaz ise şirketiniz içinde yürüteceğiniz yeniden yapılanma, iş akışlarınızın yeniden düzenlenmesi, ERP uygulamaları, verimlilik çalışmalarınız hep biraz eksik kalacak, en önemlisi hedeflerinizi yitirme ihtimaliniz yükselecektir.
Eğer bir eyleminiz değer katmıyor ise masraf yaratıyor demektir, değer katmayan eylem ve alışkanlıklarınızdan kurtuldukça maliyetiniz de azalacaktır, peki ama nasıl ?.
Seminerin İçeriği
1. Maliyet Nasıl Oluşuyor, Aşamaları ve Azaltma Yaklaşımları
2. İsrafın Tanımlanması ve Yalın Kurum İlişkisi
3. ?7 İSRAF? yöntemi ve Video
4. İSRAF’ ın keşfi ve analizi için 4 Yöntem + WorkShop
5. Süreç Analizi Çalışması Nasıl Yapılır
Kim Katılmalı
Şirket sahipleri ve üst yönetimi, yalınlaşma ekip üyeleri, planlama ve üretim yöneticileri, üretim ekip liderleri ve operatörleri, ERP/MRP uygulama grup üyeleri, maliyet muhasebesi, mühendislik ve kalite bölümü çalışanları.
Bu seminere niçin katılmalısınız
İsrafın bulunması ve yok edilmesi hem maliyet azaltma hem de yalınlaşma çalışmasının temelidir. Endüstriyel İsraf, şirketlerde boşa harcanmış olarak düşünülen bazı tüketim malzemeleri veya zamanın çok ötesinde bir analiz ve tespit metodlarına ihtiyaç duyar.
Bu seminerde, israfı nasıl hiç hata yapmadan tespit edebileceğinizi, nasıl tekrar oluşmasını engelleyebileceğinizi öğreneceksiniz.
Sertifika Semineri düzenleyen kuruluş tarafından verilecektir
Kullanılan Kaynaklar
Lean Manufacturing That Works ? Bill Carreira
Lean Transformation ? Bruce A. Henderson / Jorge L. Larco
Identifying Waste On the Shopfloor ? Productivity Press
Manufacturing For Survival ? Blair R. Williams The Toyota Way ? Jeffrey K. Liker
—————————————————————————————-
Kurum içi eğitim almak isterseniz aşağıda bulunan teklif isteme formunu doldurunuz …
Kurumsal Eğitim Talep Formu
—————————————————————————————-
Maliyetinizi mi azaltmak istiyorsunuz ?
Gerçekten istiyor musunuz ?
Sıfır maliyet konumunun gereklerini yapmaya, uygulamaya hazırsanız mesele yok … Bakalım neler yapılmalı.
İlk hazmedilmesi gereken lokma “yeni bir şey yapmadan” maliyetin azalmayacağıdır.
İkinci konu ise maliyetin azaltılmasının ucuza satın alma fikrinin ötesinde olduğunu görmeniz.
Üçüncü konu ise yapmakta veya kullanmakta olduğunuz bir şeyler eksiltilmeden maliyetin azalmayacağı.
Şimdi problemden biraz uzağa gitmelisiniz, uzayda biraz yükseğe çıkmalı ve olaya uzaktan bakmalısınız.
Örneğin aşağıda bulunan şekilde kaç adet siyah nokta var, sayar mısınız ….
Gözleriniz bozuk değil ise sayamamıyor olmanız lazım, devamlı değişen sayıda siyah nokta bir var olup bir yok oluyor. Aklınız hiç olmadığını söylüyor olabilir ama ya gözleriniz !
Şimdi kalkın masadan, biraz uzaklaşın ekrandan ve tekrar bakın, bakalım kaç nokta var ?
Az önce problemin içindeydiniz şimdi ise biraz dışında … İşte uzayda biraz yükselmenizi bunun için öneriyorum.
Evet gelelim ikinci sorumuza …
Bir canlı “en az enerjiyi” hangi konumda harcar ?
- Hareket etmiyorken değil mi ? Peki şirketinizin en az maliyet noktası nedir o zaman … Eğer siz hiç kıpırdamaz iseniz, birileri paralarını size getirip gökten aşağı inen ürünlerinizi satın alıp giderler ise ne güzel olurdu değil mi ? İşte “vizyon” bu bence ! Zaten şirketlerin vizyon cümlelerinde “ileride bulunmak istenen nokta” tarif edilmesi gerekmiyor mu ?
Şimdi vizyon bu ise “misyon” ne olmalı. Yani biz niye varız, müşteri niçin bizden alsın, bizim müşterimiz kim ?
Maliyetimizi azaltmamıza yardımcı olacak “müşteri grubunu” bulmalıyız. Eğer maliyetimizi arttıracak müşteri grubuna yakalanmış isek fiyatlarımızı gözden geçirmeye başlama zamanı gelmiş demektir. Bu aşama önemli çünkü “müşteriden başlayan” ve “geriye doğru getirilen” süreç bize bir aşama sonra yürümemiz gereken maliyet yolunu gösterecek.
Aşamalar şöyle :
1. Hedef müşteri grubunun ve beklentilerinin tarifi
2. Bulunduğumuz noktanın tarifi
3. Bulunduğunuz noktadan hedefe gidecek yol
Neyse bu kadar strateji bence yeterli, şimdi gelelim aksiyon planına, ne de olsa bize plan değil pilav lazım (bu sözü hatırlıyacak kadar eski doğumlu olanlar halen mevcut, bu özlü sözü kim söylemiş bulun bakalım).
Tedarikçiyi tatlı-sert yöntemler ise ucuza satması için ikna etmek, kaçak işçi çalıştırmak, komşu firmanın deposuna tünel açıp malzeme aktarmak, alıp ta ödememek gibi hızlı sonuç veren yöntemlerin dışında maliyet azaltma çalışmasının sürdürülebileceği bence en az iki eksen var. Çok klasik olacak ama bunlardan biri dışa diğeri ise içe dönük eylemler.
Dışa dönük olan eylemler müşterileriniz ve pazarınız ile ile ilgili. Müşterilerinize istediklerini vermeniz, onların değer vermediği konuları anlayıp ürün tanımınızdan bunları çıkartmanız sayesinde maliyeti azaltırken tüketicinin algıladığı değer artmış olacaktır. Bunun için izlenebilecek yöntemler var, örneğin “hedef maliyet çalışması”, “müşterinin sesini duyma çalışması – VOC”,”rakiplerin müşteriyi ne yönde koşullandırmaya çalıştığının anlaşılması” gibi projeler ile çok önemli adımların atılması mümkün.
İçe dönük eylemlere bakarsak liste daha uzun…
Stok, stokların yaşı, elinizde bulunan stokların hizmet kalitesinin ölçülmesi, IQR analizi, kayıt doğruluk analizi ve ihtiyaca göre yapılacak satınalma planlaması kendi başına bir konudur.
Bir diğer üretim içinde operasyonel verimlilik konusu, elinizde bulunan üretim imkanlarının kullanımını ortaya çıkartacak olan OEE analizlerini yapabilir noktaya gelmek, sonuçlarını “kayıplarınızı” azaltacak şekilde kullanmak ile önemli tasarruflar sağlanır.
Başka bir konu ise yine üretim alanında “hareket” analizi yapmak buna “standart work” çalışması da diyebiliriz. Her ne kadar biraz farklı iseler de sonuçta “işi yapma haritanız” ortaya çıkacak. Örneğin kesikli imalat uygulamasında istasyonlar arası bulunan stok sizin bu çalışmanızın önemini azaltır, konuyu soğutur. Ancak ortada bir hat var ise kayıp o hat üzerinde bulunan bütün operasyonların kaybı olacağı için konu ciddileşir.
Kayıt yapmak için harcanan süre, kayıt kontrolu için harcanan süre, süreçlerinizin içinde bulunan değer katmayan adımların keşfedilmesi ve yok edilmesi … Belki de şirketinizin her gün yaptığı 1000 eylemin 400 adedi bu sayede yok olurken yerine size daha fazla değer katacak 200 yeni adım ekleyeceksiniz … veya hiç eklemeyeceksiniz.
Müşteriye hızlı bilgi aktaran bir B2B sistemi yıllar geçtikçe büyüyen bir tasarruf kaynağı olabilir, e-satınalma, e-satış ve e-bilgilendirme sayesinde binlerce saat tasarruf sağlayabilirsiniz …
Firmalar ERP sistemlerini de buna benzer amaçlar için kurmak ister. Aksilikler ve maliyet azalsın, işler izlenebilsin, hesaplamalar daha hızlı ve kesin olsun gibi hedefler için ERP yazılımları satın alınır. Eğer uygulamayı başarırsanız faydalı da olur. İlk faydası şirketinizin büyümesi ve iş hacmi artışını mevcut kadrolarınızı çok büyütmeden karşılayabilecek olmanızdır, ERP sisteminin sağlayacağı otomasyon sayesinde bu mümkün olmaktadır. İkinci faydası ise karar verebilmeniz için daha net ve hızlı bilgi sağalayabilecek olmasıdır.
Say say bitmez … Peki niçin yapmıyorsunuz, niçin maliyetinizi azaltabilecek bir çalışmayı erteliyorsunuz, niçin iyileştirme projeleri genellikle “negatif” davranış ile karşılaşır, niçin “bizde” olmaz diye düşünülür, hatta niçin hiç düşünülmez ?
Öncelikle bunun cevabını kendinize siz vermelisiniz ama benim de ekleyeceklerim var.
Ben bu konuyu “israf” konulu seminerimde işliyorum, seminere katılanları 2 gruba ayırabilirim.
1. Hakikaten ben olaylara böyle bakmamıştım, bana ve şirketime faydalı noktalar öğrendim.
2. Ben de biliyordum bunları, peki şimdi hangi tuşa basacağım.
Aslında bu konu size anlatıldığında “evet,biliyorum” tepkisi vermeniz normal, ihtiyacınız ise bu çizgiyi aşıp yöntemi pozitif bir yaklaşım ile anlamaya çalışmanız. Zaten bir şirketin “iyileştirme” çalışmaları karşısında aşması gereken engel de budur, kısacası “biliyoruz bunları sen bize farklı bir şey söyle” yaklaşımı çok “hazır” bir tepki olduğu gibi o sırada anlatılmakta olan yöntemin detaylarını kaçırmanızdan ve sonra da “savunma” konumuna geçmenizden başka hiç bir işe yaramaz.
Diğer yandan uygulama alanında kan, ter ve gözyaşı olacağı aşikardır. Şimdi düşünsenize “öyle bir düğme olsa” konunun danışmanları size gelip o düğmeye kendileri basarlar ve bu işi yaparak onlarca kat fazla para kazanırlar. Böyle bir yol olmadığı için onlar anlatıyor ve siz de uyguluyorsunuz … İyi haber birden fazla yolunuz olduğu kötü haber ise çalışacak olmanız.
5S Niçin Yapılır
* İsraf görünür hale gelir ve eliminasyonu kolaylaşır
* Ekipman, malzeme ve çalışma alanı üzerindeki kontrolunuz artar
* İşletme içinde morali yükseltir, takım çalışmasını teşvik eder, çünkü herkes katılabilir.
* Çok geniş bir alanı etkiler :
* Ayar ? SetUp süreleri kısalacaktır
* Kalite değerleri yükselecek, harcamalar azalacaktır
* Çalışma güvenliği kesin olarak artacaktır
* Birim zamana düşen üretim ve katma değer artacaktır
5S ‘in 1. adımı : Sınıflandır
Gereksiz nesneleri çalışma ortamından uzaklaştırmalısınız.
Çalışma alanınızda bulunan ama işinizi yapmanıza bir katkısı olmayan nesneleri işaretlemeli ve çevrenizden uzaklaştırmalısınız, bunun için kullanılan en bilinen yöntem Kırmızı Etiket Yöntemidir.
Metod : KIRMIZI Etiket Yöntemi
Hangi koşula uyan nesneleri Kırmızı Etiket ile işaretleyeceksiniz ? Bir hafta (bir ay) içinde gerekmeyecek olanlar gibi bir kural koymalısınız, sonra aşağıdaki gibi nesnelere bu gözle bakmalısınız.
Fazla veya zamanı geçmiş malzeme kümeleri
Kısa zaman içinde kullanılmayacak ekipman
Zamanı geçmiş kağıt, form veya dosyalar
Efektif kullanılmayan dolap, çekmece, masa
Ne olduğu belirsiz, kutu, konteyner
Zamanı geçmiş poster, slogan, duyurular
Önce bu tür nesnelere birer Kırmızı Etiket yerleştirilir, sonra bunlar merkezi bir yerde toplanır ve tekrar sınıflandırılır. İleride kullanılmayacak olanlar imha edilir, diğerleri çalışma alanının dışında, tertipli bir şekilde depolanır.
5S ‘in 2. adımı : Sırala / Düzenle
Herşeyin ?1? yeri olmalı, yerinde olmayanın bakınca anlaşılması gerekir.
Çalışırken kullanılacak herşeyin 1 yeri olmalıdır.
Etiket, renkli alan (örneğin kullanılan araçların yerleştirildiği pano veya masanın neresinde ne bulunacağına göre etiketlenmesi veya boyanması) gibi göze hitap eden teknikler ile ?herhangi birinin? aranan şeyi bulabilmesi ve tekrar yerine koyabilmesi mümkün olmalıdır
Nesnelere kolay erişilebilmeli, operatörün fiziksel zorlanmasına sebep olmayacak şekilde yerleştirilmelidir.
5S ‘in 3. adımı : Sil / Temizle
Önce bir alanın ne kadar temiz olması gerektiğine karar verin, sonra bu noktaya ulaşana kadar temizleyin.
Bir temizlik kampanyası 5 adımdan oluşur :
Hedeflenen temizlik seviyesinin tespiti
Görevlendirme
Metodlara karar verme
Araçların temini
Takip, kontrol listeleri
Ve 3 hedefi vardır :
Bütün çalışma alanlarını temiz, aydınlık bir hale getirmek ve çalışanların moralini yükseltmek
İlk iki maddeyi sürekli gözden geçirmek ve canlı tutmak
Kirliliğin temel kaynaklarını bulmak ve yok etmek
5S ‘in 4. adımı : Standartlaştır
En iyi pratikleri günlük hayatın bir parçası haline getirmelisiniz.
Bu aşamanın amacı ulaşılan seviyenin sürekli olmasını temin edecek kurguyu oluşturmak ve bir sistematiğe kavuşturmaktır.
4 adımlık bir prosedür sürekli izlenmelidir.
Planla : Kim neyi ne zaman yapacak ?
Kaynakları Yarat : Yapılması gereken işlerde kullanılacak araç ve zamanı belirle.
Uygula : Sınıflandırma, Sıralama ve Temizleme işlemlerini günlük hayatın içinde gerçekleştir.
Denetle : Sonuçları izle, bir önceki ile kıyasla ve başa dön.
5S ‘in 5. adımı : Sahiplen ve Sistemi Koru
Bu aşama 5S ?in en güç olanıdır.
Sahiplenme aşaması 5S çalışmasının belki de en zor olanıdır. Çünkü insan doğasının değişime direnci ve her türlü sisteminde minimum enerji konumuna geçme eğilimi vardır. 5S aktif bir çalışma sonucunda başarılabilir, yeterli enerji harcanmaz ise eski duruma kolayca dönülebilir.
Bu aşamayı kolaylaştırmak için aşağıdakiler yapılabilir :
Bu çalışmanın önemi her fırsatta anlatılmalı, örnekler ile (eskiden ? şimdi) desteklenmeli,
Kontrol ve kıyaslama listeleri oluşturulmalı ve periyodik olarak kullanılmalı,
Sonuçlar herkes tarafından bilinmeli, sistem önerilere açık olmalı
Eski durum ? istenmeyen durum olarak belirlenmeli ve çalışma boyunca geçilen safhalar görsel yöntemler ile belgelenmeli, göz önünde olmalı.
Bu sunumda İsraf / Waste kavramının en yalın tarifini bulacaksınız, size farklı bir bakış açısı katacağını düşünüyorum. Bildiğiniz gibi bu tür sunumlar site üyelerine açıktır, üye olmak ücretsizdir.
Gönderi Listesi Ne Demek ? : cengizpak.com.tr sitesinin bir gönderi listesi vardır, örneğin bu sunum listemizin 10′uncu sırasındadır. Site üyelerine bunun gibi çalışmalar belli bir sıra ile gönderilmektedir. Üyelik ücretsizdir ve hemen sağ tarafta bulunan ?Bu siteye üye olmak istermisiniz? başlığı altında bulunan form aracılığı ile gerçekleştirilmektedir, sizi de aramızda görmek isteriz. Gönderi listesinde daha neler olduğunu görmek için tıklayınız >>>
5S nedir ?. 5S çalışma ortamının toparlanması, düzenlenmesi ve tekrar bozulmaması için bir dizi alışkanlığın elde edilmesine dair bir çalışmadır. 5S bütün iyileştirme çalışmalarının nerede ise ilk adımı olarak kabul edilen bir çalışma ve metod olarak düşünülebilir.
Hazırladığım sunumu ister akademik ister şirket içi çalışmalarınızda ,kaynak belirterek ücretsiz olarak kullanabilirsiniz.
Bu sunum site üyelerinin gönderim listesindedir, bu ve bunun gibi sunum, araştırma, ERP, Stratejik Planlama, Yalın Üretim Teknikleri, Tedarik Zinciri Uygulamaları gibi konular ile ilgileniyor iseniz
Bu IBAN numarası denilen şey biraz uzun, TRXX 1234 9876 5432 OOOO 1111 55 gibi bir şey oluyor. Problem ise normal yazılırken 4 hanede bir boşluk verilmesi ve dolayısı ile bilgisayar ortamında “32″ karakterlik yer kaplamasından ortaya çıkıyor. Şimdi olay şöyle oluyor :
1. Birisi birisinden IBAN numarasını istiyor, karşı taraf % 95 ihtimalle e-posta mesajı olarak yazıyor ve muhtemelen boşluklu ve 32 karakter (IBAN 26 karakter) geliyor …
2. Mesajı alan kişi bunu kopyalıyor ve banka ekranında bulunan sahaya yapıştırıyor … elbette tam yapışmıyor çünkü bankanın programcısı burasını 26 hane yapmış, IBAN ucundan kesiliyor …
3. Mesajı alan kişi şimdi arada bulunan boşlukları teker teker siliyor, geriye kalan haneleri de eli ile yazıyor.
Şimdi kaybedilen zamanı ve hata yapma ihtimalini bir düşünün. Eğer programcımız bu ihtimali düşünerek (nasıl düşünülmemiş olduğu da enteresan !) tedbir almış olsaydı herhalde 1 saniye sürecekti ama şimdi en azından 15 saniye sürüyor. 1 veya 15 saniye ne fark eder diyebilirsiniz … şimdi bir hesap yapalım.
Bir şirketin 300 cari hesabı bunların da ortalama 3 banka hesabı olsun toplam 900 eder, 900 saniye yerine 900*15 = 13 500 saniye harcanacak, bir bankanın böyle 10 000 hesabı olsa toplam 130 500 000 saniye eder diğer bir deyim ile 36 000 saat gibi bir şey, bence bu hesabın fazlası yok ama eksiği vardır … Diğer bir deyimle durumu özetleyelim. Basit bir program özelliği ile, belki programcının 1-2 saat harcaması ile toplum 36 000 saat ve bir yığın olası hatadan kurtulabilirdi … İşte israf böyle bir şey ve yok edilmesi hiç te zor değil.
Bilirsiniz bazen bir şeyin ne olduğunu tarif edebilmek için saçma sapan sorular sormak yardımcı olabilir. Bu tip yaklaşımlara bugünün canı burnunda profesyonelleri “gerçekçi olmayan şeyler ile vakit kaybetmeye gerek yok” diye tepki verirler (çoğunlukla, saçma sapan düşünecek isek biz de saçmalayabiliriz, ne var bunda şeklinde …). Peki gerçek nedir ? Ya da kime göre gerçektir kime göre değil ? …
1921 yılında Henry Ford yazdığı ?Today and Tomorrow? kitabında israf kelimesini şu şekilde tanımlamıştı :
bir hammadde veya ürünün ihtiyaçtan fazla olan kısmı israftır…
Bu tanımlama ile Henry Ford senkron üretim prensiplerini gerçekten anlamış olan ilk endüstri adamı olduğunu gösterdi.
İsraf (waste), ürün veya hizmetlerimize değer katmayan, firmanın ana hedefinde ilerlemesine destek olmayan ancak gerçekleştirdiğimiz aktivitelerin tümüdür.
7 Tür İsraf Vardır
1. Bekleme
Değer katan herhangi bir şeyin yapılmadığı boş zaman.
Örnekler :
- İnsanın beklemesi
- Makinanın beklemesi
- Bir çalışanın bir makinayı beklemesi
- Bir makinanın onu çalıştıracak olanı beklemesi
- Arıza ve duruşlara etkin müdahale olmaması
- Uzun Set-Up süreleri
- Tutarsız çalışma yöntemleri
- Gereken araç ve malzemenin olmaması
2. Taşıma
Malzemenin, ürün ve hizmetlerimize değer katmayan hareketi.
Örnekler :
- Bir malzemenin birden fazla yerde olması
- Kullanılmayan malzemenin geri dönüşü
- Malzemeyi ?üretimi yarıda keserek? kenara çekmek
- Gereğinden fazla forklift, konteyner kullanımı
- Büyük partiler halinde üretim
- Bozuk malzemenin depolanması
3. İşlem
Değer katmayan işlemler için çaba harcamak
Örnekler :
- Birleştirilebilir işlemleri ayrı ayrı yapmak
- Müşterimizi etkilemeyen iyileştirmeler
- Müşterimizin beklentilerini anlayamamak
- Gereksiz onay mekanizması
- Gereksiz formların doldurulması
- Gereğinden fazla bilgi ve dökümantasyon
- Darboğazları yönetememek
- Üretim bittikten sonra yapılan kalite kontrol
4. Stok İsrafı
Üretim veya Satış için gerekenden fazla malzeme, yarı mamül, ürün bulundurmak.
Örnekler :
- Düşük devir hızı
- Operasyonlar arası malzeme yığınları
- Fazla miktarda ?yeniden işlem? , ?tamirat?
- Yeni ürünlerin piyasaya gecikerek çıkması
5. Hareket
Çalışanların değer katmayan herhangi bir amaç için hareket etmesi
Örnekler :
- Malzeme ve Ekipman aramak
- Erişim güçlüğü (eğilmek, uzanmak …)
- Malzemelerin üretim alanından uzakta olması
- Bölümler arası gezinmeye sebep olan prosedürler
- Fazla harekete sebep olan yerleşim düzeni
- Fiziksel zorlanmaya sebep olan iş ortamı, ekipman
- Büyük depo alanı
- Satılmayacak olanı üretmek ve onun takibi
6. Hatalı Eylem veya Üretim
Bir ürün veya hizmetimizi müşteri istekleri doğrultusunda onarmak, yeniden yapmak.
Örnekler :
- Ek alan, araç ve ekipman tahsisi
- Ek iş gücü kullanımı
- Ek envanter
- Sevkiyatımızın gecikmesi, teslim tarihinin aşılması
- Daha düşük karlılık, daha fazla kayıp
- Kalitemizin sorgulanması, prestij kaybı
7. Fazla Üretim
İhtiyaçtan fazla üretmek
- Önceden üretmek
- Gereğinden hızlı üretmek
- Satılmamış olanı üretmek
- Meşgul görünmek için üretmek
- Paraya dönüşmeyecek envanterin birikmesi
- Gereğinden hızlı makina ve tezgah yatırımı
- Dengesiz malzeme akışı
- Önceliklerin ve bir planın olmaması
- Büyük parti büyüklükleri
- Ekstra saklama alanı, insan gücü
İsrafın Eliminasyonu – Masrafın Azaltılması günlük hayata farklı bir noktadan bakmayı gerektiren bir çalışmadır. Bu seminerime katılan 18 katılımcıya gösterdikleri performanstan dolayı teşekkür ederim. 12 farklı şirket ve oldukça farklı sektörleri temsil eden bu arkadaşlarıma başarılar diler, herhangi bir konuda danışmak istediklerinde benimle istedikleri zaman temasa geçebileceklerini belirtmek isterim.
Seminer hakkında daha fazla bilgi için >>>
Setup süresi, bir ürünün üzerindeki işlemi bitiren bir iş merkezinin diğer ürüne geçişi arasında geçen zamandır.Setup süresi bazen ayar bazen de hazırlık süresi olarak anılır.
Tam olarak “işlemi bitmekte olan son iyi ürün” ile “üzerinde işlem başlayacak olan yeni ürünün ilk iyi ürünü” arasında geçen süredir. Bunu şema ile açıklayacak olursak :
Setup / Ayar boyunca üretim durduğu ve ortaya satılabilir ürün çıkmadığı için israf / waste yaklaşımına göre kayıp zamandır ve azaltılmalıdır. Setup süresinin azaltılabilmesi için en temel yaklaşım SMED olarak bilinir.
SMED konusunu okumak istiyorsanız tıklayınız >>>