Aşağıda okuyacağınız yazı bu bloğu izleyen okuyucularımdan Sayın Simla Altunbay tarafından hazırlanmıştır. Sizler de yaşadıklarınızı, tecrübelerinizi bu site de paylaşabilirsiniz. Kendisine teşekkür eder, faydalanacağınızı umarım.
*
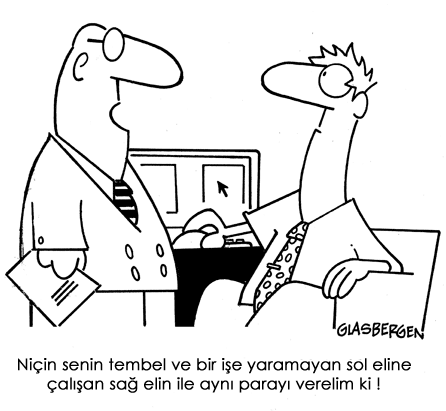
Üretim süresi içinde ekipmanın ne kadar üretken çalıştırıldığının bir göstergesi olan OEE (toplam ekipman etkinliği), basit şekilde ?belirli bir süre içindeki teorik üretim kapasitesinin % kaçını kaliteli ürüne çevirdik?? sorusuna cevap verilerek bulunabilir.
OEE bu haliyle üretimde kullanılan teknik bir analiz gibi görünmekle birlikte, süreçle ilgili sıkıntıları saptamanın etkin bir yolu aslında…
Üretim planı sıklıkla değişiyor mu?
Bundan dolayı üretim içinde önceden yapılmış hazırlıklar anlamsız hale mi geliyor?
Birbirinin tedarikçisi-müşterisi olan istasyonlar arasında malzeme ve bilgi akışı sorunu mu var?
Arızalarda tepki hızı nasıl?
OEE hesabına girmeyen ?planlı duruşlar?, gereğinden fazla uzuyor ve planlanan süreyi aşıyor olabilir mi?
Bunlara ilave edilecek diğer ?kayıpların ortaya çıkartılması ve önlenmesi? amaçlı sorularla birlikte, OEE?den hareket ederek üretim verimliliğini arttırma yönünde önemli adımlar atmak mümkün?
Kayıpların tespit edilmesi için, ekipmanın planlı ve plansız duruş sürelerini kayıt altına almak gerekiyor.
Kayıp sürelerin detaylarını formlarla kaydetmek, eğer buna özel bir otomasyon sisteminiz yoksa, başlangıç için doğru bir yöntem olabilir. Burada dikkat edilmesi gereken bazı noktalar var:
- İşletme için toplam bir OEE hesabından ziyade, çıktı bazında farklılaşan iş istasyonlarının OEE değerlerini hesaplamak, kayıpları daha net görmek için tercih edilmeli. İstasyonların girdileri, makineleri, proses adımları ve çıktıları açısından farklı dinamikleri olabilir.
- Bu dinamikler, doğal olarak ?duruş tiplerini? de etkiler. Hangi istasyonda ne tip ana duruşlar var ise, formları öncelikle bu duruşları tespit edecek şekilde tasarlamakta fayda var.
- Formların tasarımlarını, istasyonda çalışan operatörlerin fikrini alarak yapmak, ve pilot bir kullanımdan sonra eksikler varsa düzeltmek, onların da içeriği sahiplenmesini sağlayacaktır. ?Gerektiği zaman değişebilir? yaklaşımı açıklık mesajı verecektir; ancak form tasarımının sürekli değişmesi yapacağınız analizlerin önce-sonra karşılaştırmasını zorlaştırır.
- Formlardaki duruş tiplerinde mümkünse ne çok detay, ne de fazla makro bir bakış açısı olmalı.
- Formların istasyondaki operatörler tarafından ?anlık? olarak doldurulması mühim… Forma işlenmesi sonraya bırakılan her duruş, unutulmaya veya yanlış işlenmeye açık…
- Formlar doldurulurken operatörün değil, makinenin duruşlarının kaydedildiğini de ara kontrollerle teyit etmekte fayda var.
- Formların günlük olarak toplanması ve belli bir takip sistemine işlenmesi de, yöneticiler tarafından çözülmesi gereken bir problem. Bu konuda belli bir sorumlu atanacak mı? Veriler günlük mü kaydedilecek, haftalık konsolidasyon mu yapılacak? Veri doğruluğu nasıl kontrol edilecek? (Hem formlar doldurulurken, hem de bu veriler tanımlanan kayıt sistemine işlenirken hata yapılabilir.)
Form örneği:
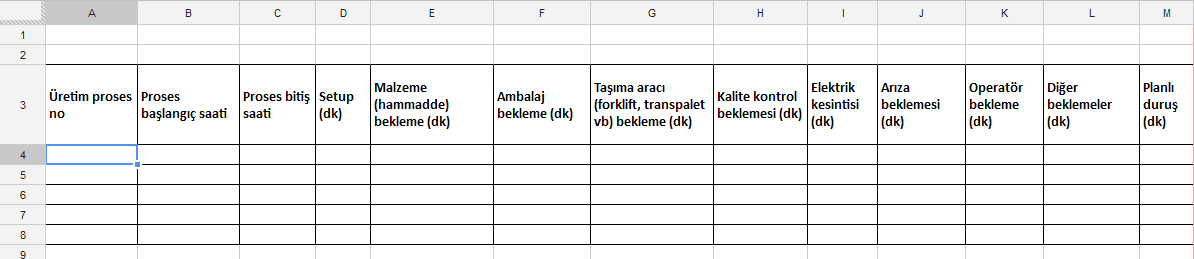
* Formu görmek için üzerinde tıklayınız
Duruş kayıtlarının tutulması, yukarıda belirttiğim gibi, kullanılabilirlik analizlerinin yapılması için önemli bir altyapı oluşturacaktır. Burada, duruş sürelerinin toplamı, bu toplamların ?toplam çalışma süresi?ne oranı, duruşların önceki günlere göre hangi seyirde olduğu, hangi duruş tiplerinin artma eğiliminde olduğu gibi tespit ve analizlerin de yapılması, iyileştirme çalışmaları için gerekli. Bu analizleri ofiste de yapabilirsiniz, formen/ustabaşlarınıza eğitim vererek onların günlük olarak yapmasını da sağlayabilirsiniz.
Kritik olan, toplanan verilerin görünür hale getirilmesi ve bu verilerin kullanılması suretiyle bir sonuca gidilmek istendiğinin ekiplere anlatılması… Yani ekiplerin, verileri boşu boşuna tutmadıklarını anlamaları?
Görsel yönetimin basit bir uygulaması olarak, iş istasyonlarına panolar yerleştirilebilir ve tutulan veriler grafikler halinde bu panolara günlük olarak işlenebilir. Verilerin panoya formenler (ileride ise dönüşümlü olarak ekip üyeleri) tarafından işlenmesi, ekiplerin bu verileri sahiplenmesi açısından doğru bir yaklaşım olur. Gün içinde belirlenecek zaman aralıklarında (tercihen vardiya başlamadan önce), 5-10 dk.lık sürelerde yapılacak toplantılarda, önceki günün duruşları ve bu duruşların nedenleri tartışılabilir. Zamanla, bu nedenleri ortadan kaldıracak çözüm önerileri de gelecektir bu toplantılarda?
Pano içeriği şu verilerin/notların işlendiği sayfalardan oluşabilir:
- Planlanan/gerçekleşen üretim miktarı
- OEE datası (mümkünse ?kullanılabilirlik?, ?kaliteli ürün oranı?, ?performans? detayında)
- Duruş nedenleri
- İyileştirme önerileri
Değerlendirme toplantılarında, üretim ekipleri tarafından bu çalışma şekli benimsenene kadar, üretim yöneticilerinin de bulunmasında fayda var. Tartışma içeriğine fazla müdahale etmeden problem çözmeye yönlendirici bir tarzda yaklaşmak, ?Bu eksiklikleri neden önceden görüp düzeltmedik arkadaşlar?…? benzeri suçlayıcı ifadelerden kaçınarak israf ve hataları saptayıp ortadan kaldırmaya teşvik etmek, ekibi motive edecek ve konunun yönetim tarafında ne kadar önemsendiğini gösterecektir çalışanlara?
Tabii esas önemli olan, bütün bu çabaların sonucunda gelişim fırsatlarını yakalamak, kaynaklar göz önüne alınarak çalışmaları önceliklendirmek ve sabırla, küçük kazanımları küçümsemeden iyileştirmeleri tamamlayarak yenilerine başlamak…
Gelişim yolculuğunuzun başarılı geçmesi dileğiyle?
Saygılar,
Simla Altunbay